[제조로봇 도입으로 디지털 전환 성큼] (2) 삼현 생산성 쑥쑥
청년 인구 감소, 기피(3D) 업종 외면으로 말미암은 노동력 부족은 전 산업계가 풀어야 할 문제다. 특히 이는 제조업이 중심 산업인 경남지역이 겪는 큰 애로 중 하나이기도 하다.
한국산업단지공단 경남지역본부·한국로봇진흥원·산업통상자원부는 이 같은 문제를 해소하고자 ‘2024년 창원국가산업단지 DX(디지털 전환)를 위한 첨단제조로봇 실증사업’을 시행하고 있다.
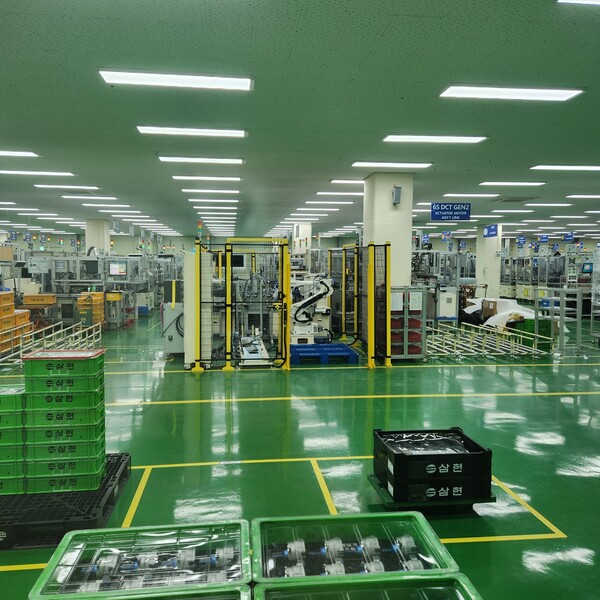
삼현의 DCT 모터 조립라인 제품 검사, 이송 공정 자동화 설비 설치가 진행 중인 모습. /삼현
◇‘삼현’ 전 공정 자동화로 불량률 제로 향해 = 창원산단 소재 자동차부품 전문기업 삼현은 ‘(유)코아시스템’을 공급기업으로 ‘DCT(Dual Clutch Transmission·듀얼 클러치 변속기) 모터 조립라인의 마지막 공정인 제품 검사·이송 공정’에 로봇을 도입한다.
총사업비는 5억 7600만 원으로, 삼현은 제품 검사와 이송 2개 공정을 모두 자동화하면서 DCT 모터 조립라인 100% 자동화를 달성하게 된다.
박기원 삼현 사장은 “조립라인에서 제품 검사에는 다관절 로봇, 비전 시스템을 투입해 불량률 감소가 예상된다”며 “이송 공정에서는 다관절 로봇, AGV(무인 운반 로봇)를 활용해 이송 중 안전사고 예방이 기대된다”고 설명했다.
기존 공정은 2명의 작업자가 작업대 앞에 서서 외관검사를 시행하는 것으로, 단순 반복작업이지만 피로가 누적되면 검사 오류가 발생할 수 있다. 더불어 검사가 끝난 부품은 팰릿 위에 쌓게 되는데, 이 부품들을 이송하는 과정에서 안전사고 발생 등의 가능성이 있기에 삼현은 이를 개선하고자 했다.
이번에 제조로봇이 도입되면서 DCT 모터 조립라인은 100% 자동화 공정을 갖추게 됐다.
먼저 제조가 완료된 제품을 받으면, 로봇이 딥러닝 비전검사를 활용해 외관검사를 수행, 품질 데이터를 쌓아가면서 불량품을 색출하게 된다. 부적합품은 따로 격리하고, 완제품은 전용 트레이에 적재하는 방식이다. 완제품이 쌓인 트레이는 정렬 작업을 거쳐 상자에 담겨 포장되고, 이 포장된 상자들을 AGV가 적재 팰릿으로 운반한다.
이번 로봇 도입으로 공정 생산성은 일일 1897개 생산에서 2100개 생산으로 10.7% 개선, 불량률 0건, 기존 2인 인력 재배치 등으로 완전 자동화를 이룰 수 있을 전망이다.
박 사장은 “ 노동자 허리, 무릎 등 근골격계에 무리가 갈 수밖에 없고 이에 공정 기피가 예상됐다”며 “더불어 측면에 스크류를 체결할 때 작업자 실수로 체결하는 홈의 위치를 못 맞추면 불량품이 나오게 된다”고 설명했다.
이어 “이번 도입으로 사이클 타임 개선부터 인력 재배치 등의 정성, 정량적 효과까지 발생할 것으로 기대된다”고 덧붙였다.
2022년 K-스마트등대공장 대표공급기업 선정, 올해 초 코스피에 상장한 삼현은 이번 사업을 토대로 조립 라인 자동화를 위해 더욱 힘쓴다는 계획이다. 또한 창원지역 신공장 증축과 더불어 제조 물량 확대를 기반으로 경남지역 자동차 부품산업 활성화에 이바지하겠다는 계획이다. <끝>
※ 이 기사는 한국산업단지공단 경남지역본부와 함께 기획했습니다.